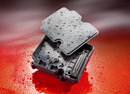
Materiał odporny na hydrolizę
Materiały stosowane w napędach samochodowych są narażone na wysokie temperatury, wilgoć i wibracje. Aby utrzymać odporność na takie warunki przez cały okres eksploatacji samochodu, użyte tworzywa muszą być specjalnie przystosowane.
Czytaj dalej
Odnosi się to również do termoplastycznych poliestrów, takich jak politereftalan butylenu (PBT), który jest używany pod maską silnika na przykład na wtyczki, złącza i obudowy elementów elektronicznych. Kontakt z wodą - nawet tylko w postaci wilgoci zawartej w powietrzu - prowadzi w przypadku poliestrów do hydrolitycznego rozszczepienia łańcuchów polimeru, a tym samym do osłabienia materiału, zwłaszcza w podwyższonej temperaturze.
Ultradur HR – PBT odporny na hydrolizę
Wprowadzając rodzinę tworzyw Ultradur HR (HR oznacza odporny na hydrolizę), BASF dostarcza odmiany PBT zoptymalizowane pod względem odporności na hydrolizę w środowisku wilgotnym. Dzięki temu materiał ten nadaje się do wytwarzania elementów, które przy szczególnie długim okresie eksploatacji działają w bardzo wymagających warunkach. Odnosi się to także do dwóch nowych gatunków Ultradur, które łączą wysoki poziom odporności na hydrolizę ze zintegrowanym uniepalnieniem i przezroczystością dla lasera, co może być pomocne w wielu nowych zastosowaniach.
Czytaj również: Bezpieczny osprzęt elektryczny w pokoju dziecka
USCAR klasa 5 – test zaliczony
Tworzywo BASF Ultradur HR nie tylko pozytywnie przechodzi testy standardowe. Równie dobrze zdaje cykliczne testy klimatyczne wymagane przez normę USCAR klasa 5. Coraz częściej uwzględniają ją specyfikacje techniczne w przemyśle samochodowym. Przestrzeganie tej normy wymagane jest na przykład dla wtyczek i złączy. Wymogi testów, jakie przechodzą komponenty, wychodzą daleko poza zwykłe statyczne testy klimatyczne. Już w przeszłości specjalnie opracowany Ultradur HR wykazał, że bez problemów znosi wilgotne i gorące warunki środowiskowe. Na rynku jest dostępny Ultradur HR z 30-procentowym wzmocnieniem włóknem szklanym, nazwany Ultradur B4330 G6 WP oraz zawierający 15% włókna szklanego Ultradur B4330 G3 HR. Obydwa gatunki są znacznie bardziej odporne na hydrolizę niż produkty bez optymalizacji HR. Wyprzedzają także konkurencyjne materiały tego typu.
Starzenie w komorze klimatycznej: bez zmian przez 6000 godzin
W celu sprawdzenia odporności na hydrolizę często stosuje się metody badań w stałych warunkach klimatycznych. Typowe warunki w testach przyspieszających to na przykład temperatura 85°C i wilgotność względna 85%. Próbki wykonane z odmian Ultradur HR umieszczono w tych warunkach klimatycznych na 3000 godzin i szczegółowo badano w stałych odstępach czasu. Stwierdzono, że wytrzymałość na rozciąganie pozostawała niezmienne wysoka przez cały okres przeprowadzania testu.
W celu określenia granic możliwości tworzywa Ultradur B4330 G6 HR test został przedłużony do 8000 godzin. Jego wyniki pokazały, że wytrzymałość na rozciąganie ulegała stopniowemu zaburzeniu dopiero po 4800 do 6000 godzin. To oznacza, że Ultradur HR jest w badanych warunkach znacznie bardziej stabilny niż wszystkie inne materiały.
Czytaj również: Czujniki w systemach klimatyzacyjnych
Badania w zaostrzonych warunkach klimatycznych: USCAR klasa 5
Istotną różnicą w testach przeprowadzanych według wymogów normy USCAR klasa 5 jest to, że ciepło i wilgoć działają na badane próbki nie statycznie, a cyklicznie. W ośmiogodzinnym cyklu próbki poddane są różnym określonym temperaturom i poziomom wilgotności atmosferycznej. W przebiegu badań zmiany tych parametrów dobiera się w taki sposób, by wilgoć pochłonięta przez tworzywo sztuczne nie miała możliwości wyparować przed rozpoczęciem fazy wysokiej temperatury. Symulacja następuje w procesie dwufazowym. Najpierw próbka jest dokładnie zwilżana w standardowych warunkach klimatycznych, następnie szybko ogrzewa się ją w tymczasowym procesie operacyjnym, albo w wyniku ogrzewania zewnętrznego, albo właściwego dla samego procesu. Stanowi to niezwykle wysokie obciążenie dla materiałów takich jak PBT. W takich warunkach degradacja zwykłego PBT spowodowana hydrolizą byłyby znacząca.
Zanim próbki zostaną poddane szczegółowej analizie, cykl ten podczas testu powtarza się 40 razy. Także w tym przypadku Ultradur HR wykazuje skrajną wytrzymałość i tylko niewiele zmienia swoje właściwości mechaniczne. Podczas gdy wytrzymałość na rozciąganie materiału porównawczego nieodpornego na hydrolizę spada w znacznym stopniu już po 20 cyklach, wytrzymałość na rozciąganie Ultradur HR pozostaje praktycznie bez zmian, nawet po 40 cyklach. Jest on zatem znacznie lepszy od konkurencyjnego produktu.
4000 godzin starzenia cieplnego i żadnych problemów
Ultradur HR spisuje się lepiej niż inne produkty, nawet w warunkach suchych i gorących. Dowodzą tego badania na starzenie, którym poddawano Ultradur B4330 G6 HR w stałej temperaturze 150°C przez 4000 godzin w specjalnej komorze. Przeprowadzone następnie testy mechaniczne wykazały, że udarność utrzymywała się na stałym wysokim poziomie. Natomiast udarność z materiału porównawczego bez HR spadła gwałtownie do niskiego poziomu. Wysoki poziom odporności na starzenie cieplne jest ważny, gdy elementy są ogrzewane do wysokiej temperatury za pomocą ogrzewania zewnętrznego lub własnego w długich okresach czasu. Ultradur HR wytrzymuje stałe obciążenia w wysokiej temperaturze szczególnie dobrze w środowisku suchym, co sprawia, że doskonale nadaje się do zastosowań w wysokiej temperaturze, na przykład do elementów w komorze silnika.
Nowe możliwości zastosowania w samochodach elektrycznych
Dzięki temu znacznie rozszerzonemu profilowi właściwości Ultradur HR może być stosowany tam, gdzie PBT do tej pory nie był brany pod uwagę. Na przykład, duża stabilność cieplna wraz z dobrze znanymi właściwościami elektrycznymi PBT może być interesująca dla komponentów pojazdów elektrycznych. Należą do nich wtyczka do ładowania, obudowa akumulatora lub wtyczki obwodu wysokiego napięcia w samochodach elektrycznych.
Stabilny i prosty w przetwarzaniu
Ultradur HR jest nie tylko odporny na hydrolizę. Charakteryzuje go też stabilna lepkość stopu. Zapewnia dobre warunki przetwarzania nawet w wysokich temperaturach i stosunkowo długim czasie trwania procesu. Zoptymalizowana lepkość stopu zapobiega zjawisku powstawania na elementach nieestetycznie nakrapianej powierzchni, znanemu jako efekt marmurkowy. Ponadto niska jest także tendencja materiału do tworzenia pęknięć termicznych, podobnie jak ryzyko zablokowania kanałów wtryskowych, które mogłoby prowadzić do przerwania produkcji.
Nowe gatunki: trudnopalność i przezroczystość dla lasera
BASF pracuje obecnie nad rozwojem kolejnych gatunków tworzywa Ultradur stabilnych hydrolitycznie. Najnowszym jest Ultradur B4450 G5 HR. To nowe rozwiązanie łączy w sobie odporność na hydrolizę ze zmniejszoną palnością, wysoką odpornością na prądy pełzające i niską gęstością dymu. Jest to profil właściwości opracowany m.in. pod kątem pojazdów elektrycznych. Ponieważ przepływ prądów jest znacznie wyższy w zespole napędowym pojazdów elektrycznych niż konwencjonalnych, stosowane elementy muszą przejść ponowną analizę pod kątem spełniania wymogów bezpieczeństwa.
Inny nowy gatunek tworzywa łączy odporność na hydrolizę i przezroczystość dla lasera. Jest nim Ultradur B4300 G6 HR LT, który ma przezroczysty dla lasera czarny kolor oraz określoną przezroczystość dla lasera podczas spawania laserowego. Zastosowania obejmują w tym przypadku między innymi obudowy sterowników lub czujników. Są one spawane laserowo z kilku części i muszą być odporne na hydrolizę.
Źródło: basf / budnet.pl
Komentarze
Tagi
Czytaj też…
Czytaj na forum
- Jak pozbyć się zapachu papierosów? Oczyszczacz pow... Liczba postów: 59 Grupa: Budowa i re... To może zamienić takie klasyczne tytoniowe papierosy na te elektryczne? ich ogromny plusem jest właśnie brak nieprzyjemnego zapachu. Nie znam wśród znajomych ni...
- Listwa otwarta na remont Liczba postów: 16 Grupa: Budowa i re... Sähkön hintaan vaikuttavat useat tekijät, joista merkittävimmät ovat sääolosuhteet Nord Poolille sähköä toimittavissa maissa. Tuulivoiman kasvava osuus sähköntu...
- magazyn Liczba postów: 550 Grupa: Firmy budow... Firmą specjalizującą się w produkcji i dostarczaniu wysokiej jakości hal przenośnych jest https://best-idea.pl/bloczki-i-klocki-be tonowe.html
- Bloczki z betonu komórkowego a chłonność wilgoci. Liczba postów: 5 Grupa: Budowa i re... Jeśli szukasz firmy świadczącej usługi w zakresie technicznej obsługi inwestycji budowlanych, specjalistycznych badań i orzecznictwa w sprawach budowlanych a ta...
- Dekorator wnętrz Liczba postów: 296 Grupa: Firmy budow... Watch bigg Boss 19 online free only on official website. {url="https://biggboss19watch. com/"}bigg boss 19{/url}